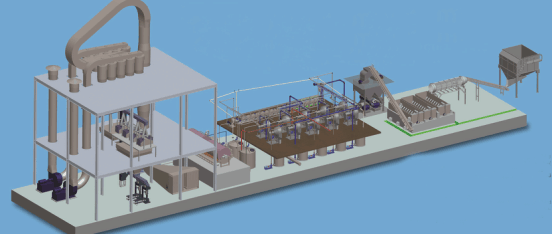
sample analyzing
- sample analyzing
- cleaning and washing
- rasping and milling
- cyclone de-sanding
- centrifugal extracting
- refining
- solid - liquid separation
- drying and screen
- weighing and packaging
BRIEF INTRODUCTION ABOUT SUBCRITICAL EXTRACTION TECHNOLOGY:
In recent years, subcritical extraction technology becomes a newly-developed separation technology with the development of supercritical extraction technology. “subcritical fluid” refers to the extraction solvent obtains similar physical nature as supercritical fluid when approaching the critical state. On circumstances that extraction solvent is in full contact with material, by control of extraction temperature and pressure, lipid from raw material will be selectively extracted and separated. As compared to conventional extraction techniques, it features low extraction pressure (1.2mpa), low extraction temperature, low equipment cost and energy consumption, no residue of solvent due to volatilization, and better retention of heat-sensitive components in final products. Thus it can be considered as a green, eco-friendly & sustainable developing technology. The technology is very suitable for extraction from materials in bulk quantity and seasonal intervals like pepper skins, seeds and etc., with high value. It has a wide range of applications in phamaceutical, food, flavors and fragrances, biotechnology and other industries.
Extraction solvent adopts efficient & eco-friendly refrigerant 134A, it’s non-toxic, safe, non flammable, volatile, solubility thus is particularly suitable for the extraction of oil and heat-sensitive materials.
Subcritical fluid extraction technology not only to overcome the traditional method after pressing need to extract oil refining process cumbersome, oil nutrients and yield loss is large, and an organic solvent extraction separation process required to separate distillation heating, oil oxidation, rancidity, etc., but also reduce the high production costs of supercritical CO2 fluid extraction disadvantage, the extraction process is simple and efficient, economical and practical, especially for food industry extraction and separation of biologically active substances and heat-sensitive material, can greatly keeping extract natural qualities, technology has significant advantages.
1. TARGET PRODUCTS EXTRACTION
1.1 Extracting & refining of lipid-soluble pigments such as lycopene, capsanthin, xanthin and etc.
1.2 Functional oil: tomato seed oil, chili oil, grape seed oil, pepper oil, sea buckthom oil, perilla seed oil, linseed oil, coconut oil, palm oil, pepper oil, walnut oil, almond oil, pumpkin seed oil, cumin seed oil.
2. FEATURES OF SUBCRITICAL EXTRACTION TECHNOLOGY
2.1 Rated pressure of complete system is 1.6mpa, actual working pressure is less than 1.3mpa, the entire extraction process flow can be done at relatively low pressure safely.
2.2 As a result of relatively low pressure requirements, compared with supercritical co2 extraction method greatly reduces the effective volume of the device manufacturing process difficult process and the project cost, the device can be in multiple zoom, safety system performance relative increase.
2.3 Due to non-flammable , non-toxic solvent extraction, etc., can ensure that the system uses normal process conditions and process extraction production environment, do not require special precautions.
2.4 The boiling point of the solvent extraction -26.18ºc, can be completely volatilized at room temperature, with the use of other process for the purification treatment, solvent residues in the finished product is less than 5ppm, 50ppm much higher than the national standard.
2.5 Since the solvent extraction of fat-soluble substances with good solubility, therefore, the active ingredient in the raffinate retained low levels, it can generally be controlled below 0.4%. If the increase in the number of extraction, the residual raffinate flow may be less than 0.1%.
2.6 The use of low boiling point solvent extraction properties, by reducing the degree of vacuum in the process , so that rapid evaporation of the extraction solvent at a temperature of 10 ºc to 50 ºc in order to increase the solvent recovery, while effetively avoiding “heat sensitive” component loss and damage as much as possible to save the active product active ingredients, improve product quality.